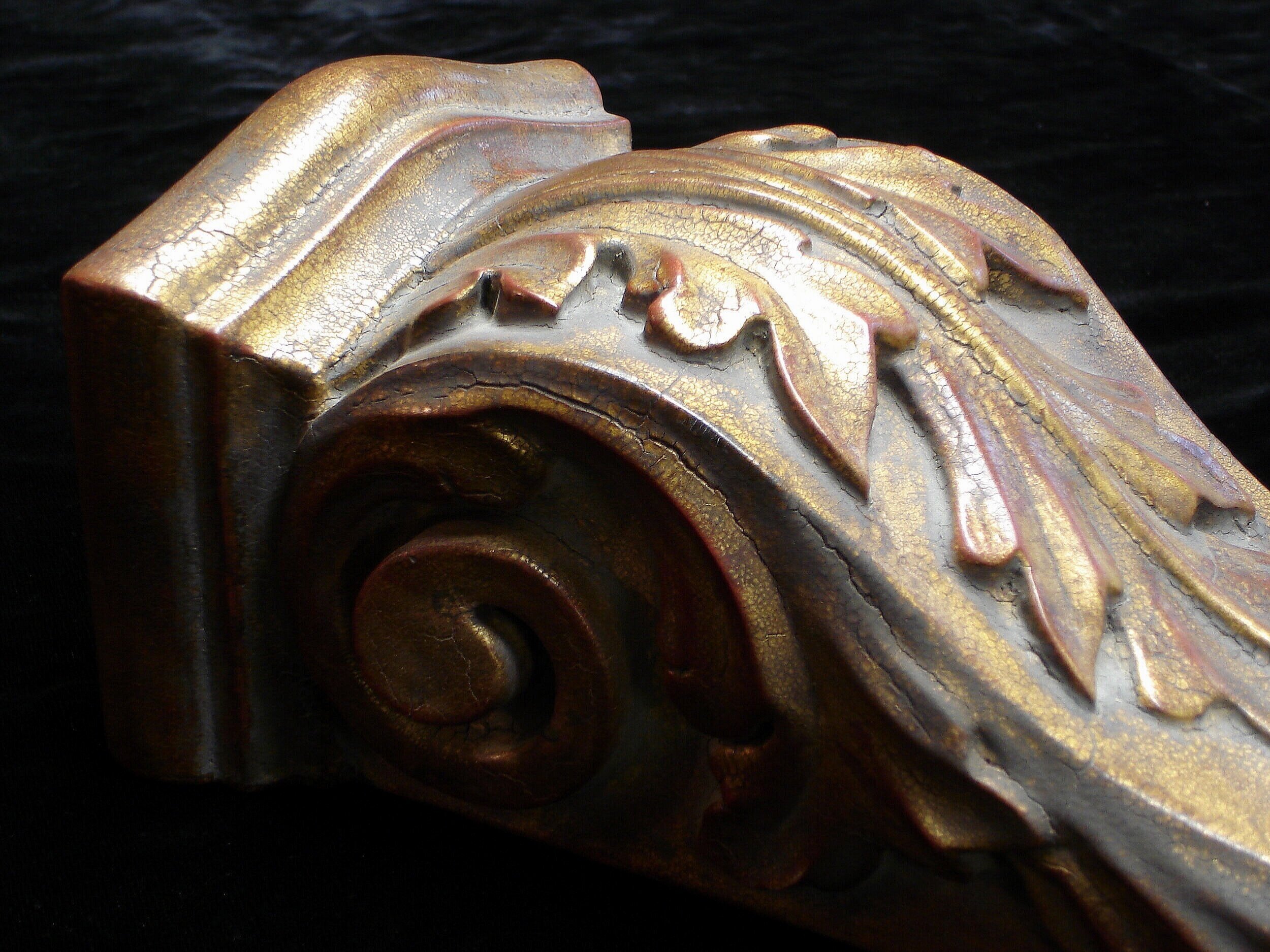
Gilding: An Historical Narrative
The Art of Gold Leaf Gilding…
Leafs of gold applied to objects for ornamentation goes back over 4,000 years ago to Northern Africa where gold foil was applied to wood to give the appearance of being made of solid gold.
The practice of gilding in the Middle East, whereby gold would be applied over other metals, has been traced to at least 3,000BC and continues to this day. Tomb paintings in Egypt as early as the VI Dynasty (around 2250BC) depict goldbeaters beating gold into foil, used in the decoration of furniture and coffins. Historical references indicate fire gilding of gold on copper in China by the fourth century BC. Still other applications include gilded statuary in fourth century BC Athens, gilded vessels of Tibet in the seventh century AD, and various gilding techniques and applications throughout South America, Peru, Spain, the Far East, Britain, and Europe.
Gilded architectural embellishment adorned not only the palaces and temples during the time of Cleopatra but is also evident today throughout Europe and in contemporary buildings and residences in the United States. Some of the finest gilding, however, took place in early 18th century France when Louis XIV desired to show his power through the gilt works of his time, establishing France’s leadership in the decorative arts.
The Process of Gilding Wood: An Overview
Mordant Gilding and Traditional Water Gilding
The methods of gilding used today are rooted in ancient Egypt and later refined during the Renaissance. There are two methods of gilding wood: Traditional Water Gilding and Mordant Gilding; the terms refer to the manner in which the leaf is applied.
Oil gilding, one of the primary mordants, incorporates the use of an oil-based size, or varnish, over a prepared ground. Another popular contemporary size is an acrylic emulsion sold as water-based adhesive which works in a similar way as oil size though with its own working properties. Once the oil size or acrylic emulsion dries and comes to a slight tack, the leaf is laid onto the surface and gently compressed with a pounce pad or brushed with a soft brush. After the size has dried, any loose particles of leaf, or skewings, are wiped off and the gilded object may then be given a clearcoat of shellac for protection against light handling while gently subduing the brilliancy of the gold. Toning with various patinating materials may also be used at this stage to simulate age or to provide contrast. As with traditional water gilding, both genuine gold and silver leaf may be used in mordant gilding as well as brass leaf, aluminum leaf, palladium leaf, platinum leaf, white gold leaf, and others. A mordant gilded surface is singular in its tonal quality and offers a matt to moderately bright appearance depending upon the type of size used and the length of time that passed in waiting for the size to reach the desired tack - the lighter the tack the brighter the gild, the stronger the tack the more matt in appearance of the leaf. It is a durable finish but unlike water gilding, it cannot be burnished with an agate stone.
Historically, other mordants derive in part from the Vegetal kingdom and aqueous in nature when prepared including Gum Ammoniac, Garlic Juice (Ilinocopia), Glair (beaten egg white), as well as Fish Glue, among others.
Traditional Water Gilding, the most highly regarded form of gold leaf gilding for frames and furniture, is a time consuming process but captivating to watch as the thin leafs of gold, measuring a thickness of only 1/250,000th of an inch, flutter through the air at the end of the gilder’s sable hair tip and laid over a meticulously prepared surface. When considering the gilding of a frame, the frame body is first milled, cut to size, joined, sanded, and then coated with a protein binder, most often rabbit skin glue. A white, plaster-like material called gesso is prepared using whiting (calcium carbonate), glue size, and water and applied over the entire surface of the frame. The purpose of the gesso is to fill the grain of the wood and to provide a smooth surface to gild and later burnish. Numerous coats of gesso are applied, at least five or six although sometimes as many as twenty, depending upon the particular gesso recipe, the architecture of the design, and the overall effect the gilder wishes to achieve. Once the gesso has dried it is then sanded, or re-cut, to remove all irregularities.
Clay bole, consisting primarily of hydrous aluminum silicate, is measured in specific proportion to glue and water, reaching a consistency of heavy cream. After being heated in a water bath, the bole is brushed over the frame using anywhere from one to five coats. When dry, the bole is ready for gilding. There are many shades of bole that may be used including ochre, red, black, orange, blue, and green, imparting various tonal affects under the layer of gold leaf. Pre-mixed bole may be used or dry clay bole cones can be custom tumbled to ensure purity. Bole is imported from countries such as France and Germany and mixed with purified water, turned slowly over stones in a ceramic vessel, resulting in a silky smooth texture. Historically, different countries have used different color boles and color combinations, a consideration that needs to be addressed during restoration and conservation of gilded antiques as well as in the creation of replicas where historical accuracy is required.
At this point the gilder is ready to apply the gold leaf. Gilder’s liquor is prepared, which is simply water, a small amount of glue and alcohol (some gilders omit the glue or alcohol). The gilding water is flowed over the clayed surface several times and the gold leaf, which is picked up with a flat sable or other soft haired brush known as a tip, is then laid quickly but gently on the wet clay. The leaf is drawn around the surface or ornament by capillary action of the water. It is important that water does not touch the topside of the gold; otherwise it will cause an unsightly stain.
Burnishing gold leaf during water gilding is accomplished by polishing the gold with a very smooth stone until the leaf becomes almost dark from its own brilliance. Burnishers come in a variety of shapes and sizes, made to conform to the various contours of ornamental surfaces, coves, and flat sectioned panels. The tool, with its hard wood handle, holds the burnishing stone at the end with a metal ferrule. Agate stones and hematite are most commonly used today although Cennini in his 15th century treatise on painting and gilding, Il Libro dell’Arte, spoke of using dog’s teeth for burnishing, the shape of which most popular burnishers are presently made.
Water gilded gold leaf presents a beautiful satin tone where left unburnished, offering an attractive contrast to burnished highlights. There is some historical precedence, however, where the entire surface of a gilded frame would be fully burnished to a high luster. Centuries ago before the advent of electricity, the brightness of water gilded gold leafed frames, furniture, and architectural embellishment reflected the ambient light in a room, often best experienced under the warm glow of candlelight.
Today, tastes have evolved where antiqued gilded finishes are often desired. There are many approaches a gilder may take to simulate age. The gold leaf may be abraded or rubbed to imitate the effects of wear from handling or cleaning which would have removed some of the gold leaf, revealing the color of the underlying clay bole and overlaps of gold leaf which form the almost bamboo-like appearance around the perimeter of a water gilded frame. Umber and pale gray washes are sometimes used over an entire piece to tone down the brilliancy inherent in gilding while also giving it an aged appearance. Resins such as dragon’s blood and gamboge as well as pigments and dyes may be added to clear, orange, or ruby shellac for tonal effects. Although stories abound where chains and other tools are used for distressing in the fabrication of an antique reproduction, it is best for the aspiring gilder to view authentic old frames in museums to study the appearance of natural wear and patina, providing one can discern the genuine antique from the sometimes expertly crafted replica.
The actual laying of gold leaf is one of the areas in gilding requiring the most skill and dexterity. Evidence of gilding during the Baroque period, approximately early 17th to mid 18th century, shows a more haphazard method of laying gold leaf compared with that done in the latter part of the 18th century during the neoclassical period. This may be due in part to advancing skills but it should also be recognized that the evolution of decorative styles towards simpler and more graceful designs required greater control and symmetry in the way leaf was laid.
Gilding Glass And The Art of Verre Églomisé
The use of gold or silver leaf on glass goes back to early Roman times and was a popular technique used for Looking Glass Mirrors during eighteenth and nineteenth century England .
Verre Églomisé, the practice of reverse gilding and etched painting on glass incorporating gold and silver leaf, is the foundation for the gilded mirrors offered by Charles Douglas in his Whidbey Island gilding studio.
Each precious leaf is applied by hand and adhered to the back of glass with a gelatin and water solution. When dry, the gold or silver leaf is very gently rubbed and sealed in black paint. The effect is mirror-like with the lap lines between each leaf fully apparent.
For a distressed look (as shown in the above photograph) the strength of the gelatin size is prepared slightly weak to allow the leaf to abrade when rubbed with cotton, revealing the black backup paint when the mirror is viewed from the front. An umber-black tinted shellac speckled pattern may be applied before the glass is gilded for additional effect .
All karats of gold and white gold as well as genuine silver leaf may be used for glass gilding as it is for water gilding and oil gilding including 6k, 9k, 12k, and palladium being the most popular. All leaf is selected for its high quality and imported from such countries as Italy, France, England, Germany, and Japan.Various glass thicknesses and optional beveled edges are available, with quarter inch thick glass recommended for mirrors. ~
For those interested in learning any of the above gold leaf gilding techniques and methods, please visit the section Book a Gilding Class to browse through the variety of ongoing gilding classes that are offered Online on Zoom and In-Person. You will find several shorter Masterclasses on such topics as Pastiglia and Sgraffito as well as longer gilding courses including Traditional Water Gilding, Glass Gilding/ Verre Églomisé, and Oil Gilding.